Embrace the Power of Robotic Welding
Are you still manually welding?
Skill Standardization: Manual welding relies on the skills and expertise of individual welders, which can vary. With automated welding, the welding process is standardized, reducing the dependency on specific skill sets and ensuring consistent weld quality across different operators.
Increased Productivity: Automated welding systems can operate continuously, resulting in higher productivity compared to manual welding, which is subject to human limitations and fatigue.
Consistency and Quality: Automation ensures consistent weld quality, as the parameters are precisely controlled and maintained throughout the process. This leads to improved product quality and fewer defects compared to manual welding, which can be affected by variations in the welder's technique.
Improved Efficiency: Automated welding systems can perform welds at a faster rate than manual welding, reducing production time and increasing overall efficiency. They can also perform complex welds with precision, eliminating the need for time-consuming manual adjustments and setups.
Scalability and Flexibility: Automated welding systems can be easily programmed and adapted to handle various welding tasks and different part sizes. They offer the flexibility to adjust welding parameters and accommodate changes in production requirements, allowing for scalability and versatility in manufacturing processes.
RoboArc is Precision Redefined: Harnessing the Potential of Next-Gen Automation
Harnessing years of hands-on experience, we have developed RoboArc, an exceptional automated system that tackles downtime challenges inherent in competitor systems, driving performance to new heights.
Innovative H-Frame Structure: Optimized using FEA (Finite Element Analysis) Efficient material usage while meeting design requirements Exceptional rigidity, minimizing deflection at horizontal axis centers
Enhanced Maintenance Accessibility: Increased access panels for easy maintenance Effective cable management with protective outer shell covering Reduces wear and tear, ultimately minimizing maintenance and downtime
Precise High Precision Assembly: Utilization of dowel pins for accurate component alignment Ensures concentricity among H-frame structure, robot, pedestal, slew-ring, turntable, and more Eliminates accuracy variations due to inertia loading effects
Sealed Radial Bearing Tail-Stock Design: Extends service period with improved durability Servicing possible without removing from the frame structure Enables easy adjustment and alignment without shims
Advanced Safety Features: Safety Area Scanner provides comprehensive area scanning, surpassing light curtain capabilities High-visibility indicator lights employing fork truck safety light technology Enhances operator awareness and safety

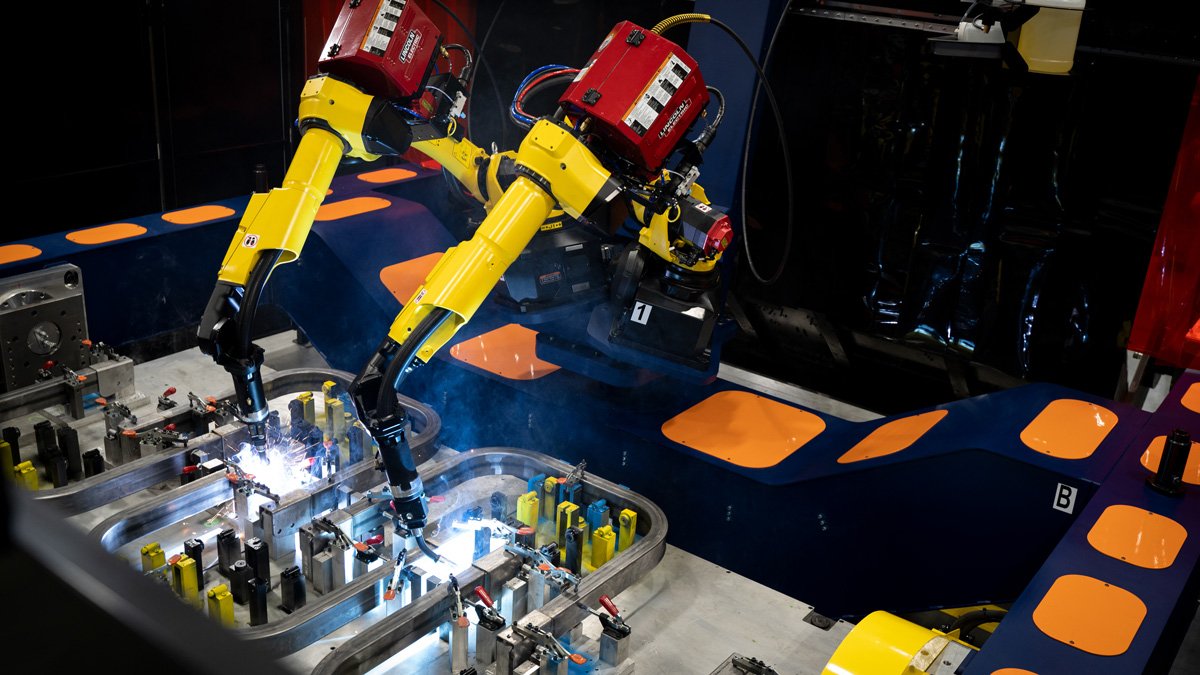
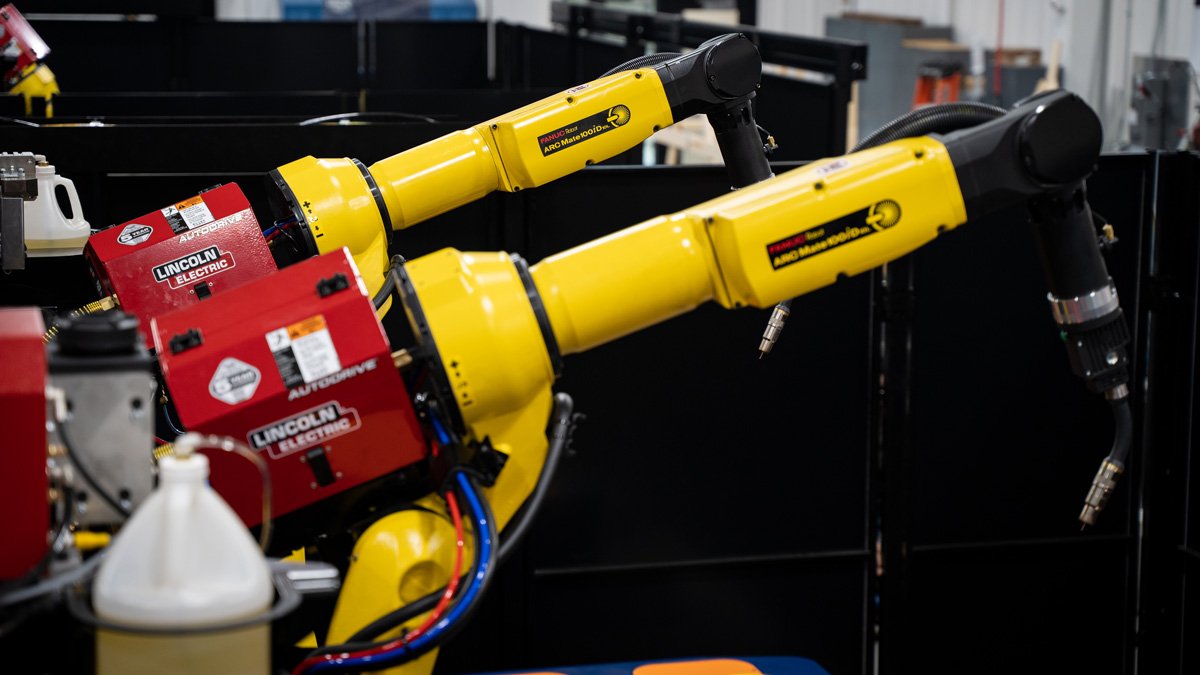
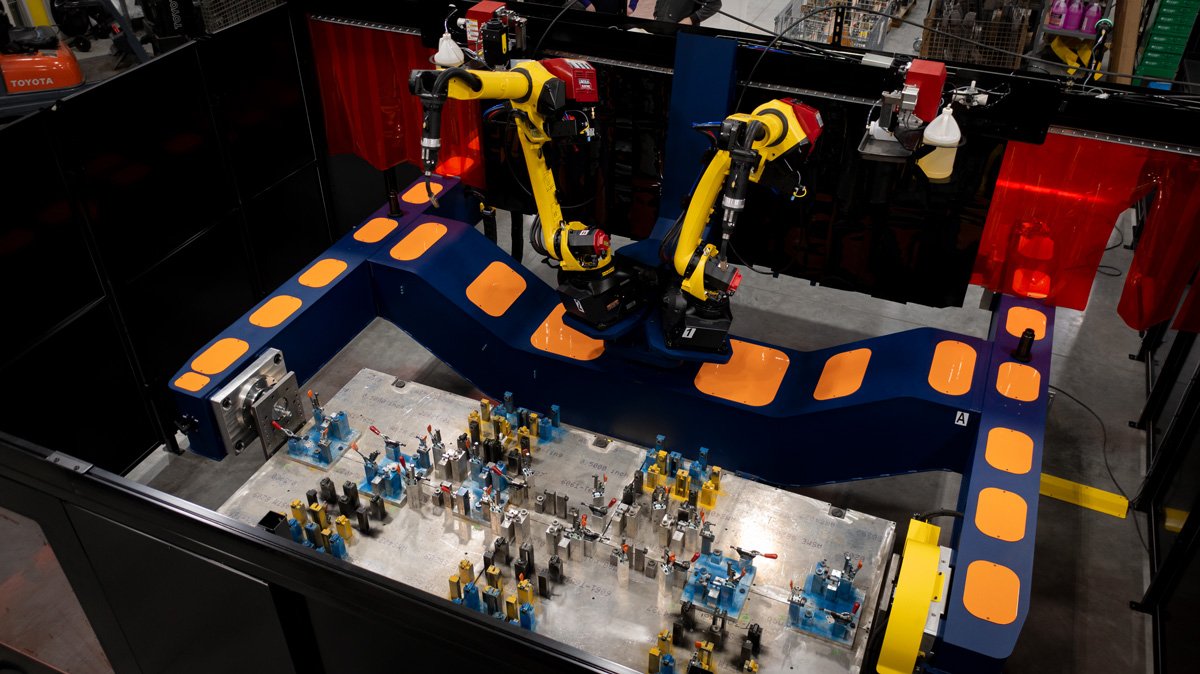
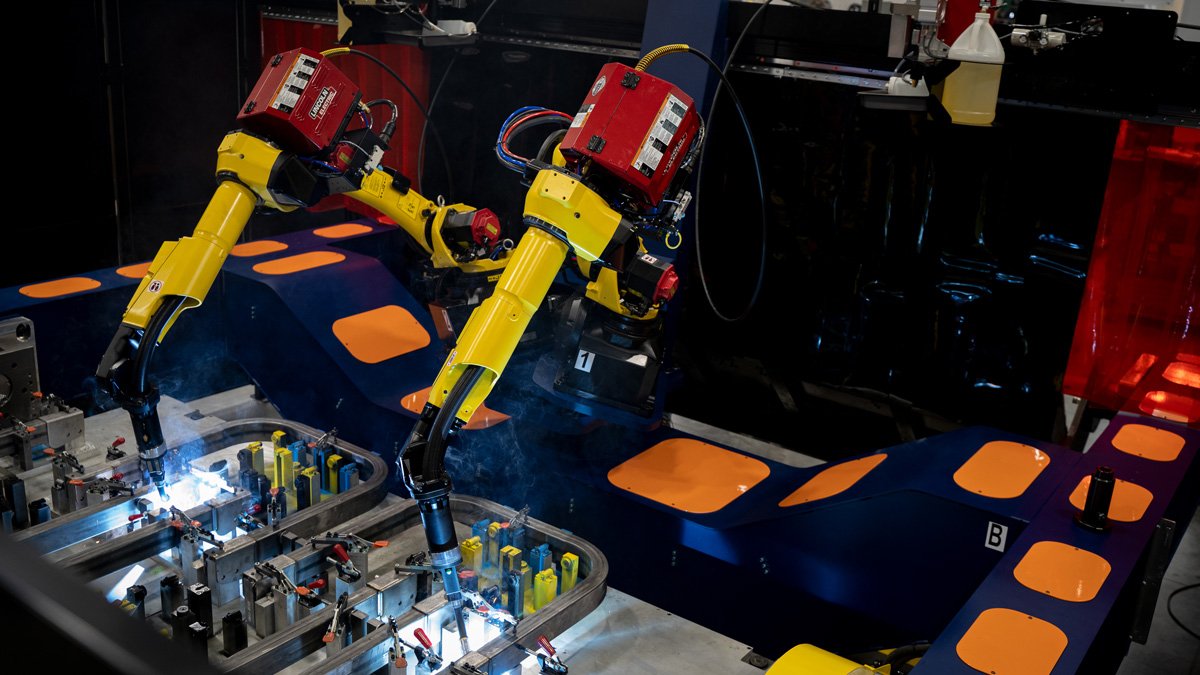
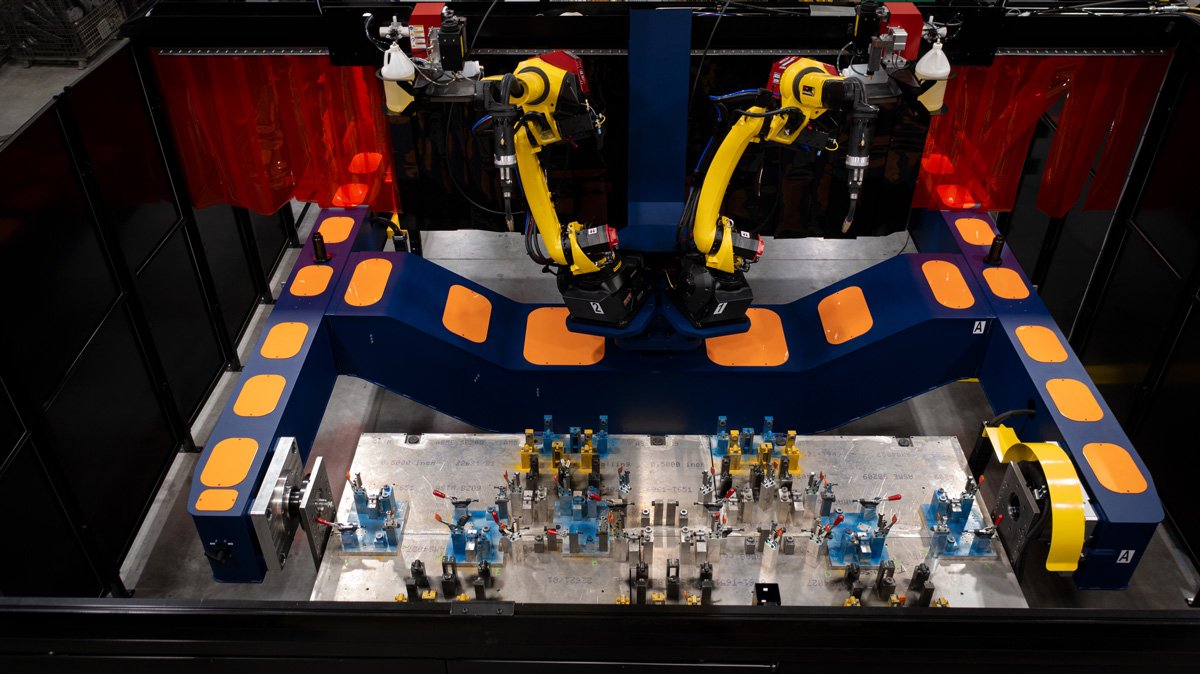
““Metalcraft Automation Group’s RoboArc robotic welding solution is by far the best system on the market. In only a short amount of time since installation, we have already noted increases in efficiency, quality, and safety. Operators comment on how easy to use the system is, and how their work environment is better because of it. Our maintenance teams have also commented on the easy access they have to components and cables to make their jobs easy for their routine preventative maintenance duties. We look forward to integrating more RoboArc welding systems into our other facilities down the road!”
”
Ignite a Bold Transformation in Your Workplace with Automated welding
To learn how Metalcraft Automation Group can improve your manufacturing processes, contact us today!